XVR Close-Up: Falck and XVR training in the cloud
Falck Fire Services Nederland (Falck) will be using the cloud to train their Fire Services using the XVR Simulation platform in several locations around the Netherlands. Falck Nederland were looking to expand their training and assessment toolkit with simulation-based scenarios, and with XVR in the Cloud, they have found a solution that is scalable, efficient, and easy for each Fire Services team to work with independently and without acquiring heavy-duty hardware. Commercial Manager of Falck Fire Services Nederland, Berthil van den Poll, says everyone is enthusiastic about the possibilities of using XVR to train virtually and in the cloud.
Falck Nederland is currently working on an ambitious pilot project to get each Falck location ready to take up virtual training with XVR On Scene. By conducting their trainings through the cloud, they run XVR’s software on virtual machines, accessible through any internet browser. This gives users the flexibility to run sessions from any PC or laptop with an internet connection from wherever they want, and without having to invest in expensive hardware for each user within the organisation.
The project was initiated by Anton van de Goor, teamleader at Kijfhoek, and Michiel Steegmans and Alwin Dillen, team member/crew at Kijfhoek, the latter of which has been the main driving force due to his experience with XVR’s platform in a previous role. The team is busy building a localised environment for each of Falck’s Fire Services locations based on maps and pictures from the industrial sites and their surroundings to make them easily recognisable for the teams in each location. They are even creating any objects needed that are not currently available in the XVR object library. Each team will initially receive one scenario, moulded on a standard exercise from each location, to get started training incidents such as fire and hazmat. The advantage of XVR On Scene scenarios is that they are easily customisable, and instructors can create incidents of varying severity and with different learning objectives by adjusting factors such as wind speed or type of hazardous material, thereby being able to offer multiple types of trainings with just the one scenario. Going forward, Anton van de Goor and Alwin Dillen’s team will be providing remote support as well as building any new scenarios requested from their colleagues. They will also be training at least 2 operators in each Fire Services team to ensure the availability of staff with the appropriate skills to conduct trainings using XVR.
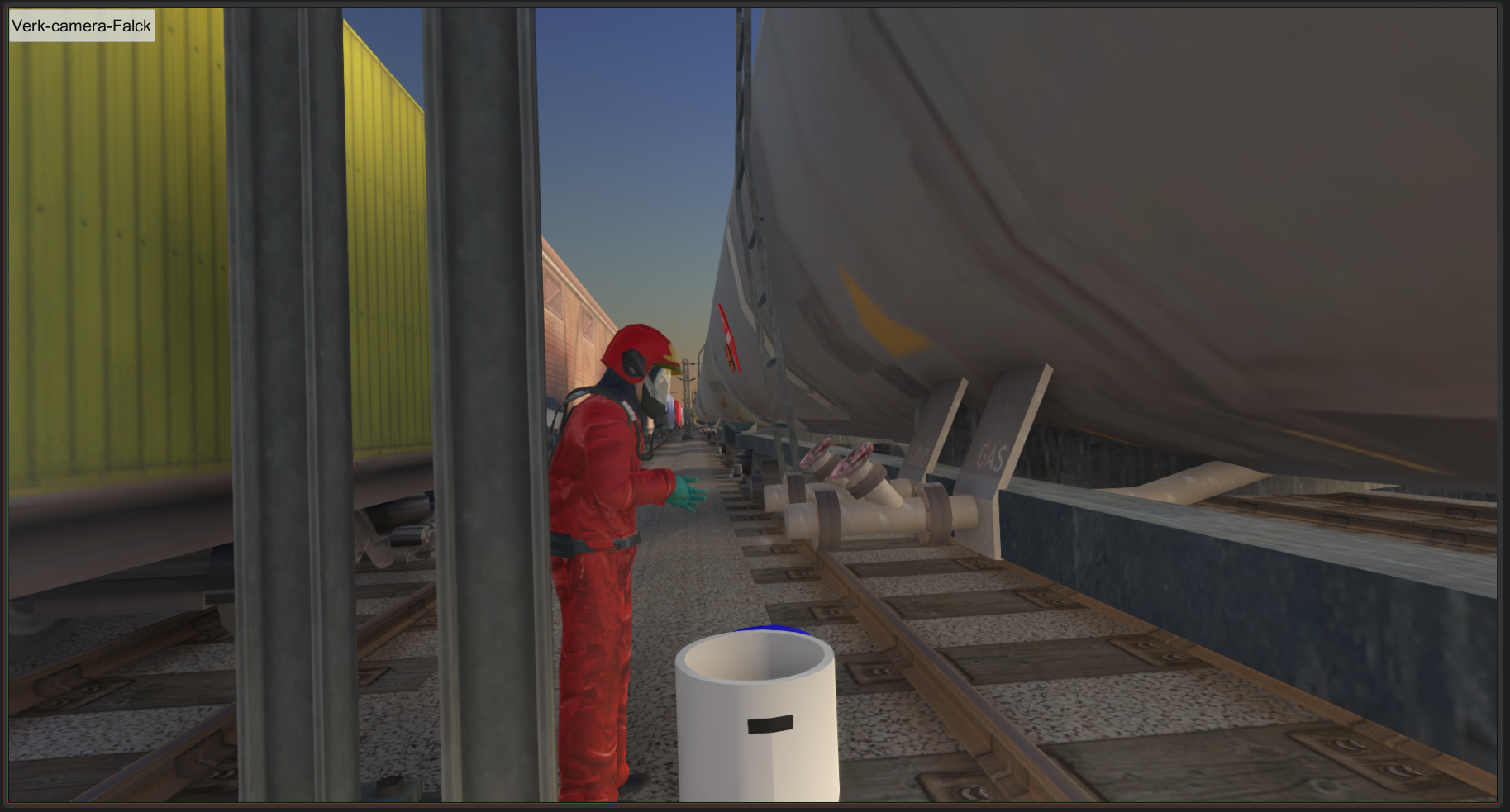
Falck Nederland provides firefighting services to several industrial locations in the Netherlands, such as the Heineken Brewery in Zoeterwoude, the chemical park Delfzijl, the chemical park in Emmen, and the Kijfhoek and Waalhaven shunting yards close to Rotterdam. Falck Fire Services are responsible for training the incident commanders and crew working at each location, but since all locations are always in operation, conducting live exercises can be tricky without disrupting the daily business. A solution to this was to train virtually using XVR On Scene. “If we are to train in live surroundings, we would be doing so on industrial premises, which are always running,” explains Berthil van den Poll. “So for us, it’s easier to train complicated scenarios, such as railyard incidents or industrial fires, virtually. That way, we don’t disturb our customers’ business processes.” Anton van de Goor adds, “If we want to conduct a live exercise involving leakage of hazardous materials from a train in the Kijfhoek, we would be putting almost all freight transport in the Netherlands on hold, as most freight trains pass through that railyard. But by using XVR, the client doesn’t have to close down parts of the track, we just access the localised railyard incident virtually. In this way, incident commanders still meet 80-90% of their requirements for that exercise.”
Berthil van den Poll says that he has long received requests internally for expanding their training tool kit, and while he acknowledges that they have not been as quick to jump onto the virtual training bandwagon as others, they are making up for lost time in enthusiasm. He believes the project got off to such a flying start because it came from the work floor instead of a boardroom – and because he sees Anton van de Goor, Michiel Steegmans and Alwin Dillen being so dedicated to the project’s success. He foresees that training with XVR’s computer-based simulations will be a very nice addition to their training curriculum. “The most important thing for us is to have competent staff, and they need to be prepared for anything that could happen on an industrial terrain”, says Berthil van den Poll. “You need to test your knowledge through assessments; you need to train your skills by completing exercises; and next to that you need to maintain your competencies. XVR covers both skills and competencies, and so it provides an easy way of training procedures without having to go outside. That’s why we find XVR On Scene to be a nice addition to what we’re already doing. We actually use it for our own quality improvement, and using it in the cloud means it’s more efficient to use and easier to roll out to multiple locations. So this was a really good option for us.”
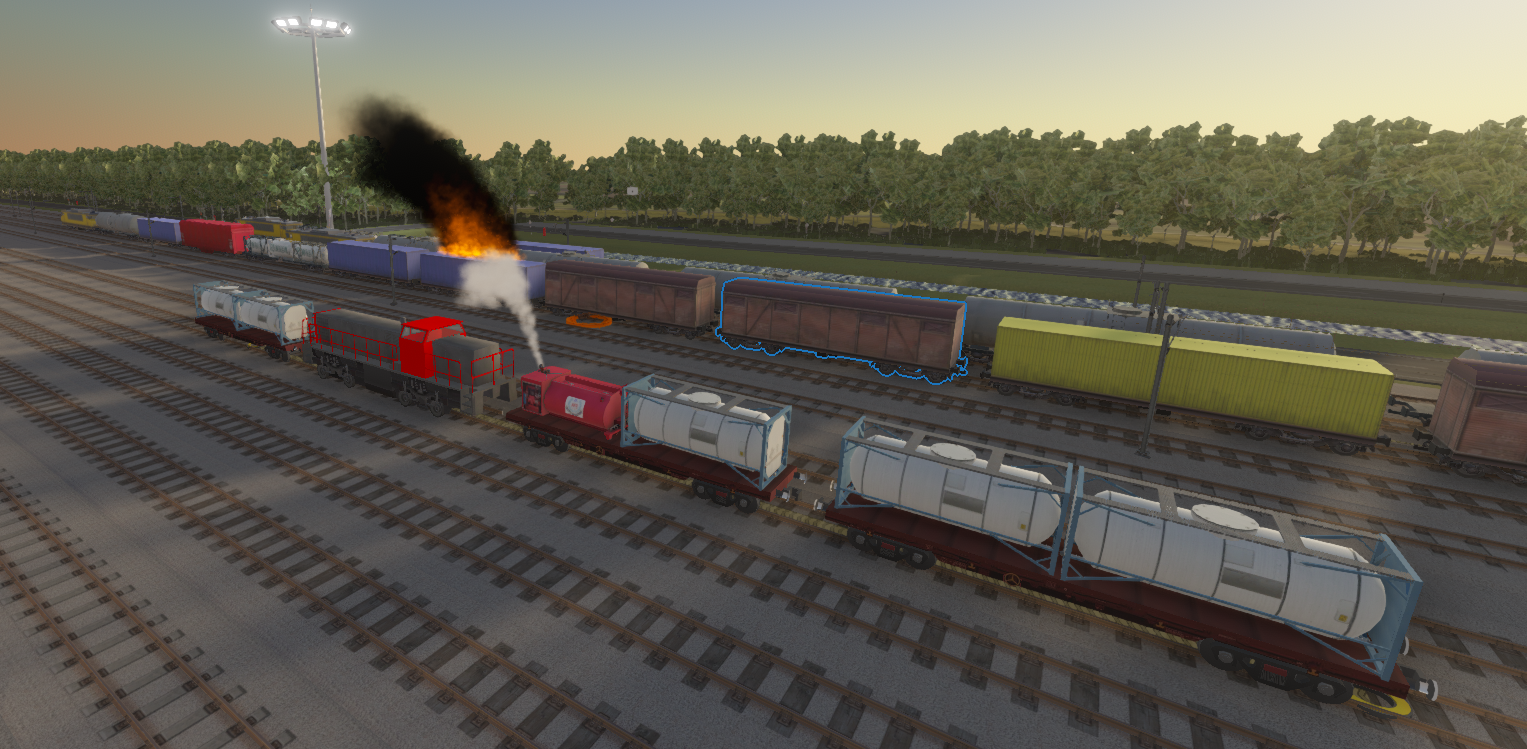
Anton van de Goor and Alwin Dillen are putting a lot of effort into carefully considering the content and processes they are creating. “If you want to build a good solution that is future-proof, then you need to think ahead. Sometimes so many things are interconnected that if we don’t make the right decisions now, it’ll come back to haunt is in 6 months or a year, and then we need to start over,” says Anton van de Goor. For this reason, they are trying to anticipate situations in which colleagues may struggle and provide clear instructions for how to use XVR’s platform in an effective and efficient manner.
With XVR On Scene, users have the freedom to create any custom scenario, depicting their unique surroundings, to fulfil their desired learning objectives. Therefore, it is important to always be clear on what exactly you want to achieve in each session. Says Alwin Dillen, “Otherwise people start to improvise, and that’s not the intention. The feedback and reactions from the instructor, and within the scenario, should always be the same, regardless of who is running the session. You also don’t want to figure out what the narrative should be as you go along, or your learning objectives will be all over the map. That’s why I find using scripts so important.” The pair are therefore developing empty scripts which their colleagues can fill in when they request new scenarios, forcing them to consider what kind of training they want to conduct and why. Their aim is to ensure that any instructor or operator can pick up a scenario and run it in the same way every time; that each participant has the same training experience and receives the right feedback; and that there are clear expectations of what the learning outcome should be.
In the future, they would also like to create more scenarios based on past incidents. Alwin Dillen explains, “One thing I think will be interesting going forward is that if you have an industrial incident – and obviously you hope that won’t be the case, but if you do – you’ll be able to recreate that as a simulation, and the customer will be able to gain insight and learn from that as well. I think there’s a lot of value in that, for the programme but also for us.”
Chemical Cluster Delfzijl will be the first of the first four locations to start their training efforts via the cloud. The expectation is that this will take place in April. If the roll-out goes well, Berthil van den Poll sees the potential to expand the project beyond the Dutch borders.
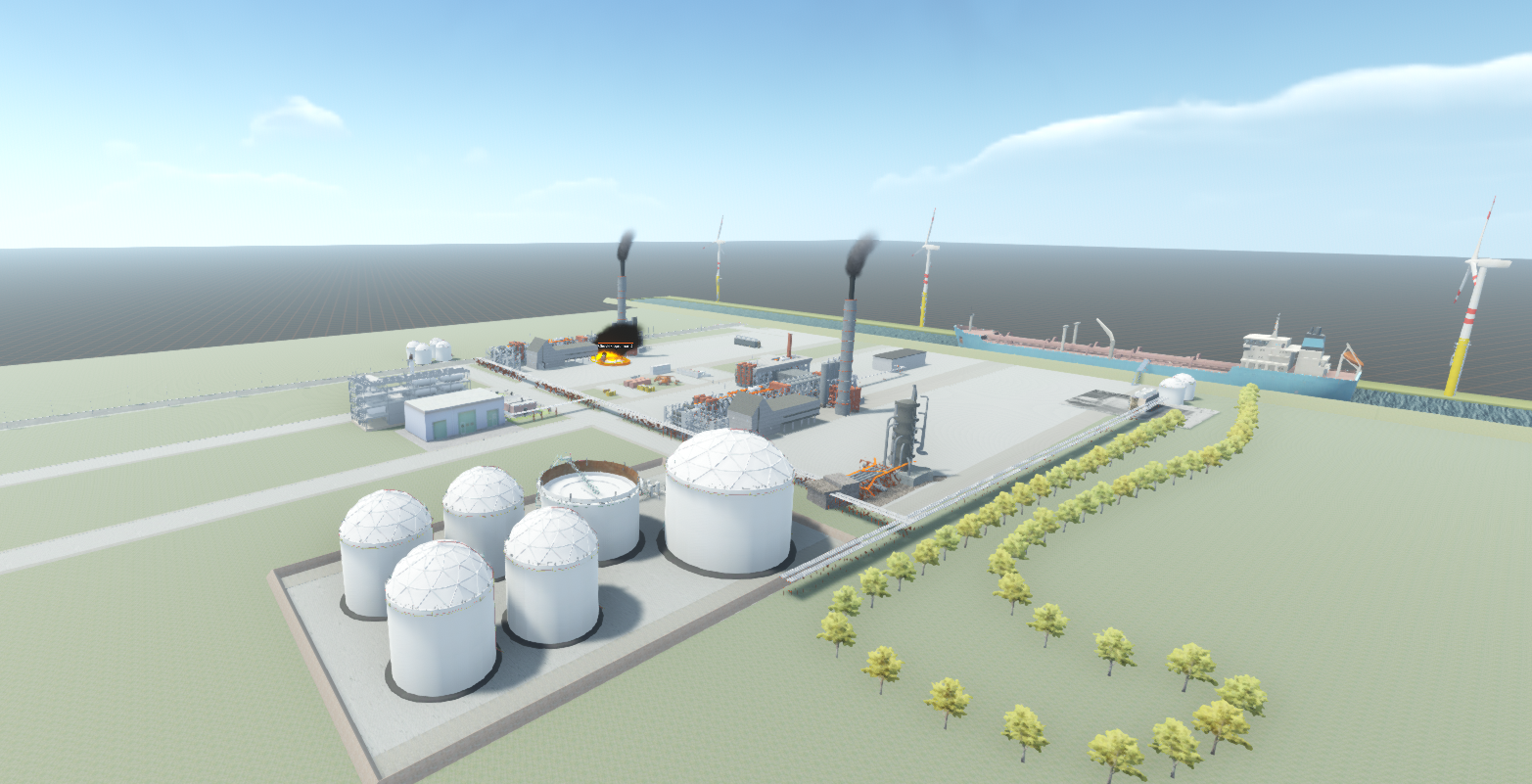